Dunque ecco che, complice un inverno per niente clemente e assenza o quasi di altri lavori impegnativi da fare per Paperoga, ci siamo documentati sul web e ci ha incuriosito molto una soluzione abbastanza convincente per piegare i tubi in acciaio. Qui altri metodi
Costruire i rulli in legno non è stato semplicissimo ma alla fine e con l'aiuto di un amico falegname ci siamo riusciti.
I rulli sono di compensato , il più piccolo ha un diametro di 30 cm ma ai fini del funzionamento potrebbe essere anche più piccolo. Il più grande è quello che determina il raggio di curvatura e , nel nostro caso , ha un diametro di 42 cm (raggio di curvatura 21 cm). Sul bordo deve essere inciso un solco che contenga la metà del tubo da piegare.
Per il rullo piccolo abbiamo usato un tornio per scolpire l’incavo, purtroppo il rullo grande non entrava nel tornio ed abbiamo dovuto improvvisare con i pochi attrezzi a nostra disposizione.Con una fresatrice abbiamo inciso un solco di ¼ di circonferenza nel bordo poi abbiamo capovolto il disco e inciso l’altro ¼ di circonferenza . Purtoppo la fresa a nostra disposizione era troppo piccola ed abbiamo dovuto lavorare ulteriormente il solco con fresette da trapano e carta vetrata.
Inizialmente abbiamo tagliato i due dischi da un pannello di compensato spessore 3 cm visto che il tubo da piegare era da 25mm in modo da avere un bordo che ritenevamo potesse essere abbastanza spesso.Una volta creati i solchi ci siamo accorti che i bordi erano molto sottili ed abbiamo deciso di attaccare uno spessore di rinforzo su entrambe le facce dei rulli di 1 cm di spessore semplicemente forando e imbullonando tutto insieme anche per dare maggiore robustezza al rullo.
Sul rullo grande va applicata una striscia di alluminio larga circa 4 cm ,spessore 3 mm in modo che abbracci il tubo il più precisamente possibile e che faccia da fermo per il tubo stesso. (può essere anche meno larga di 4 cm, noi avevamo quella di recupero purchè sia in alluminio quindi facile da modellare e curvare intorno al tubo per dare la forma desiderata.
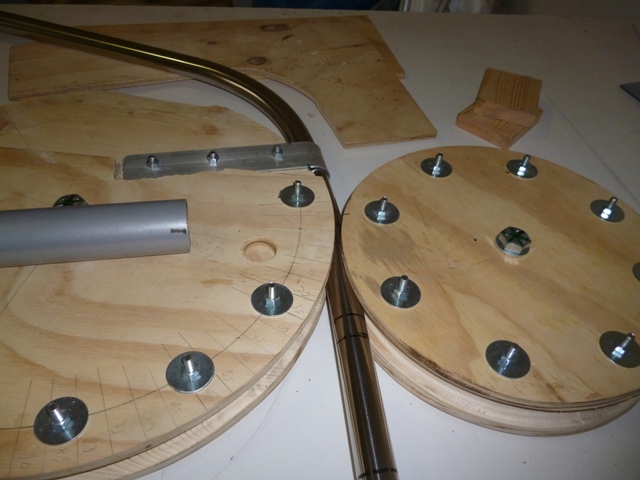
Il tutto va montato su un tavolo robusto o comunque fare in modo che non si muova, noi abbiamo messo due staffe fissate al muro con degli stopper (detti anche fisher)
Su questo quindi fissiamo il rullo grande in posizione “comoda” per fare leva e il piccolo abbastanza vicino da tenere il tubo da piegare abbastanza stretto ma comunque scorrevole. È molto importante che il buco nei rulli sia perfettamente centrato e perpendicolare altrimenti la rotazione non sarebbe in asse.
Per calibrare la curvatubi inseriamo un tubo dritto facendolo scorrere tra i due rulli e poi nella sede di alluminio e facciamo ruotare il rullo grande finchè non va in tensione il tubo. Se tutto è montato bene il punto dove i due rulli sono più vicini corrisponde a 0° di curvatura. Da quel punto ,con l’ausilio di un goniometro,segniamo i settori sul rullo grande che ci serviranno per poter ripetere con precisione le curve. Noi abbiamo scelto 5° per settore ma si può effettuare una lettura anche più “fine”.
A questo punto abbiamo installato una leva sul rullo grande e il gioco è fatto. Le forze in gioco sono piuttosto grandi quindi i vari perni e bulloni sono dimensionati per eccesso. Perni centrali da 14 mm , 3 bulloni da 6 mm per tenere la striscia di alluminio e altrettanti per la leva. A questo punto possiamo cominciare a piegare.
Abbiamo fatto un progettino con un software di grafica 3D tenendo in considerazione le misure prese sulla barca e il raggio di curvatura fisso a 21 cm. Avremmo potuto fare 2 curve da 90° alla distanza giusta e sarebbe stato semplice, veloce e...brutto. Ovviamente le cose semplici non ci piacciono e abbiamo optato per 2 curve da 60° agli estremi e 12 curve da 5 ° a intervalli regolari per l’arco lungo in modo da avere una curva ampia.
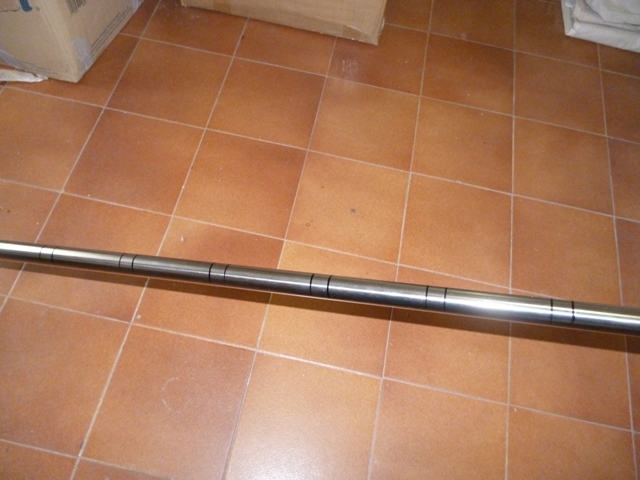
Abbiamo preso le misure e riportate sul tubo, inserito il tubo tra i rulli e fatti coincidere il primo segno con lo 0° e da li si comincia a fare la prima curva poi si sposta il tubo sul punto successivo e si curva e così via.
Mentre si fanno le curve è molto importante che il tubo rimanga ortogonale e ben in piano altrimenti si svergola. è utile anche mettere un tassello di legno avvitato allineato al rullo piccolo in modo che il tubo scorra anche contro di esso oltre che contro il rullo sempre allo scopo di mantenere il tubo in asse.
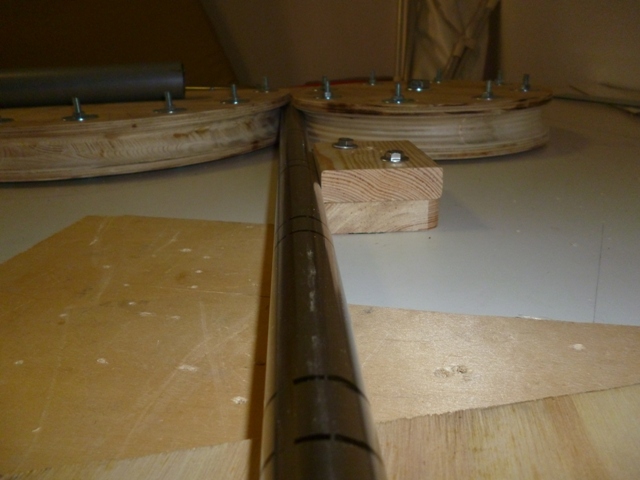


Il risultato è strepitoso!!! con modestia parlando... ma questo meccanismo permette di curvare tubi in acciaio inox senza la minima deformazione e di fare curve con qualsiasi angolo o raggio di curvatura si vuole ( per il raggio di curvatura basta fare il rullo principale più grande o più piccolo secondo l'esigenza)
Lista dei materiali
- Compensato 3 cm di spessore 35x35 cm e 45x45 cm comprato al brico pezzi di scarto dei tagli (15 euro)
- altro compensato da 1cm per rinforzare lo avevamo di scarto di altri lavori
- viti, dadi e rondelle acciaio (non 316) 2 bulloni da 14 + 20 da 6 totale 20 euro
- piastrina di alluminio 3mm anche questa avanzo di altri lavori ma quanto può costare? pochi centesimi...
- pezzo di tubo per inserire una leva e tubo per fare leva abbastanza robusto anche questo materiale di recupero
- tubo di acciaio inox aisi 316 lucidato a specchio diametro 25 x 1,5 x 6m comprato all'ingrosso dei metalli pagato 54 euro.
- raccordi e attacchi per montare lo spray hood 45 euro
Totale 134 euro contro i 400 euro del fabbro... e ho detto tutto!!!
è avanzata una metrata di tubo, stiamo pensando di saldare all'arco principale per fare un tientibene.
Prossimamente fase 2: realizzazione della copertura... se trovo in vendita una macchina adatta.
Inoltre ora avendo la piegatubi c'è da sbizzarrirsi... tendalino, gruette, e quant'altro possa servire...
4 commenti:
E bravi! Gebniale codesto attrezzino... poveri 'fabbri ladroni'!
Avete intenzione anche di cucire lo sprayhood?
ovviusly ;-) prossimamente su questi schermi... cucitura telo per sprayhood!!
Complimenti e grazie per l'articolo
Bravi!!! Certo ci vuole uno spazio dedicato...grazie
Posta un commento